Labels for Safety, Visual and Facility ID Desktop Printers
6 steps to a standardized lockout tagout program
Get benefits beyond compliance – standardize for safety and time savings
Lockout tagout compliance continues to appear on OSHA’s Top 10 Cited Standards list year after year. The majority of those citations are due to a lack of proper lockout procedures, program documentation, periodic inspections or other procedural elements. But, it doesn’t have to be this way! A little standardization of your lockout tagout programs can go a long way in ensuring the safety of your employees and your overall compliance of the regulation.
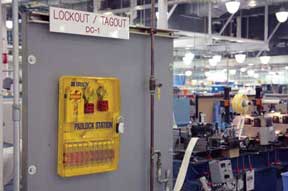
What's the benefit of standardizing your lockout tagout program?
You and your facility benefit from standardizing your lockout tagout program by:
Establishing consistent expectations
Whether it’s across departments or facilities, consistent expectations drive behavior to meet the minimum set criteria. For example, by setting a standard audit schedule that works for your business, it sets expectations that all procedures will be updated and reviewed by that date every year.
Simplifying training
Employees often move to other departments or take on responsibility for additional pieces of equipment. A standardized program that outlines the locks to use and where they are located, as well as where the procedures are located, helps to speed up the training process and aids in retention.
Reducing time spent on audits
Creating a standard template for all of your procedures helps save audit time by ensuring all critical information is located in familiar areas.
Increasing accountability
A program standardized across departments or facilities provides a global view of your lockout tagout program that makes it easier to track on the corporate level, including the proper maintenance of the program at each location.
Improving usage and safety
When employees become knowledgeable and familiar with the process, it encourages more use and helps promote a safety culture among employees’ peers.
Fostering a consistent safety culture
By giving employees a voice in the process of standardizing your lockout tagout program, you’ll create internal advocates who will naturally foster a consistent safety culture.
Getting started with standardization
Getting started is sometimes the hardest part. Before you can start on your standardization journey, it's important to ensure your current program encompasses the six key elements to a successful lockout tagout program. Of course, if you don’t have a written process already created, that should be your first step before standardizing.
Where to standardize
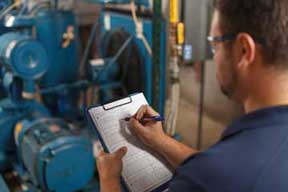
Standardized lockout tagout programs are most successful when they reach as far and wide as practical. Often times, a standardized program is only restricted by the scope of your responsibility.
For instance, if you’re a Safety Manager within a plant you may focus on all applicable departments and trades within the plant (e.g., electricians, maintenance, plumbing, etc.) that land under your responsibility. Whereas someone responsible for multiple facilities would include each facility in their standardization efforts.
This even rings true for those who are responsible for multiple facilities in different countries with different languages. In this situation, it’s important that the program is translated to accommodate the facilities in those countries. Yes, the regulating bodies are likely different for each country. While it’s important to comply with the local regulation, a best practice is to adopt and standardize the more stringent regulation your facilities encounter when writing your policy.
What to standardize
The standardization process can seem daunting when you’re just getting started. Here are the places we’ve found standardization to be the most beneficial:
- Regulatory body — such as determining which regulatory body to follow across global facilities
- Written policy/program — creating a standard policy / program for use within all departments or facilities. This can include standardizing the format or template for the written procedures
- Responsibilities — defining who’s responsible for maintaining the program at each location, who has the authority to modify and update procedures, and / or who provides training or any necessary recurring training over and above the minimum requirement
- Schedules and audits — setting the timing for audits and annual procedure reviews
- Hardware — determining what locks, tags and devices will be used, as well as where those devices are located, stored, tracked, etc
How to standardize your lockout tagout program
1. Define the regulation your organization will follow.
While each country has its own set of standards, the best practice is to apply the stricter policy throughout your organization to ensure compliance, and add an extra level of safety to your program. It’s also important to note that many larger countries such as France, Spain, Germany, Italy, Austria, Switzerland and the United Kingdom have their own safety directives (BSI, DIN, CEN) that have largely been built on OSHA standards.
- United States — In the U.S., the predominant governing regulation is OSHA 1910.147 — The Control of Hazardous Energy. If you are in the Power Generation, Transmission and Distribution industry, then OSHA Regulation 1910.269 pertains to you.
- Canada — The standard to follow derives from the Canadian Standards Association – Control of Hazardous Energy — Lockout and Other Methods, which is recognized by the Canadian Center for Occupational Health and Safety.
- Europe — The regulation varies by country, but there are some common standards such as EN 1037, which discusses procedures to deal with energy isolation to prevent equipment from being re-energized.
2. Create a written program to address the breadth of your lockout tagout scenarios.
Your written program should include:
- Procedures for outside personnel or contractors
- Continuity of lockout during shift or personnel changes
- Emergency procedures for removing lockout
- Group lockout and / or maintenance situations involving more than one person
- Assignment of responsibility (who are the authorized employees to perform lockout, responsible persons for implementing the LOTO program, enforcing lockout tagout compliance, monitoring compliance, etc.).
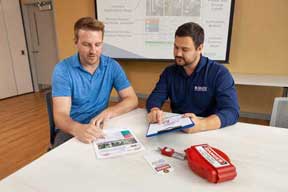
This is also a great opportunity to outline who will monitor and document any necessary and required training, as well as who will provide the training. While your written program doesn’t necessarily need to name names, it should at a minimum identify the job functions or titles of who is responsible (e.g., Site EHS Team Lead, EHS Manager, etc.).
OSHA requires the written procedures to be periodically inspected at least annually. As part of your standardization, you should set a recurring date for inspection — possibly at a time production may be at a low point for a seasonal business, after regular kaizen events or following a move of machinery and equipment. That way, your teams can plan for the same timing every year.
In the U.S. in states with their own OSHA plan, it’s important to weave any differences between the Federal and State programs into your written plan.
As an addendum to your written program, it’s also suggested you complete an asset list or listing of machinery / equipment by location.
3. Use a consistent template for all lockout tagout procedures.
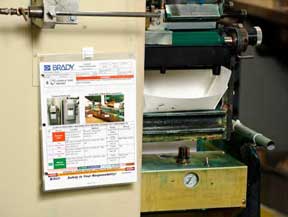
Going beyond compliance, we recommend creating best practice procedures that include machine-specific photos identifying energy isolation points. These should be posted at the point of use to provide employees with clear, visually intuitive instructions. It also:
- Encourages familiarity
- Saves times
- Streamlines audits
Investing in a software program, such as Link360, can further streamline your procedures by making it easier to create consistent and multilingual visual procedures across all of your facilities. It also gives you access to detailed program reports by site area and can be accessed from your desktop, tablet or mobile phone.
4. Create uniform, consistent schedules.
Uniform and consistent schedules not only help ensure the program is properly maintained, they also help make sure the annual audit is completed on schedule. They can also:
- Support sustainability and continual improvement initiatives
- Improve your resource planning
- Enhance coordination between departments
- Promote your safety culture
5. Standardize your hardware.
An effective lockout tagout program is most successful when it includes the complete safety picture – locks, tags and devices, as well as proper lockout procedures, program documentation, employee training, periodic inspections or other procedural elements.
- Selecting the right lock options — The correct padlock is determined by your application scenario. With a variety of material options, keying types, unique key codes and order sizes, customization, and charting available, your safety padlocks should fit the needs of your program.
- Selecting the right devices — There are a variety of lockout device options made for different energy isolation points. Once you’ve determined what device you are going to use for each isolation point, using that same product at every location reduces the chance of confusion during use, and makes it easier to maintain your written lockout tagout procedures.
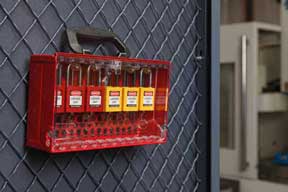
6. Provide training.

Adequate training for employees is important to communicate the processes and ensure your program runs effectively. Training should include not only OSHA requirements, but also your own specific program elements, such as your machine-specific procedures. Site-specific training should be tailored to the following categories:
- Authorized training — Specific to the employees who perform the lockout procedures on machinery and equipment for maintenance. This will be the most in-depth training that should include program-specific elements.
- Affected training — Specific to those who do not perform lockout requirements, but use the machinery receiving maintenance.
- Awareness training — For employees who do not use the machinery, but are in the area where a piece of equipment is receiving maintenance.
Next steps
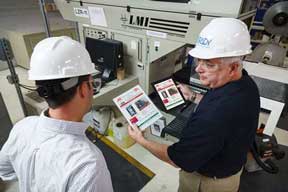
Standardizing your lockout tagout program not only ensures you’re compliant, it also streamlines your entire process by making it easier to maintain, simplifying training and improving overall usage and worker safety. While standardizing your program may feel daunting, there’s help available.
Brady provides a start-to-finish solution, which means we can jump in and help at any stage of your lockout tagout program development. Rely on our in-house team of industry experts to work with you to create a sustainable and compliant safety program supported by:
- Our insights — Field engineers from different backgrounds provide a variety of perspectives and find potential safety gaps others won’t
- Our services — Industry-trusted expertise in lockout tagout, arc flash and confined space to keep you and your team protected.
- Our products— Safety products and software designed by experts and engineered to perform
Learn more about our lockout tagout solutions at www.bradyid.com/safety-services/lockout-tagout.
Padlock Guide
Padlock Selector Tool
Resources
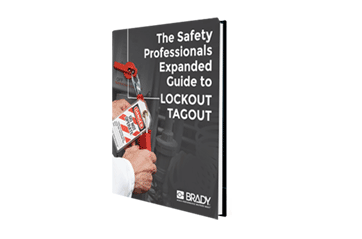
Learn more about Lockout Tagout compliance with “The Safety Professionals Expanded Guide to LOCKOUT TAGOUT”
Download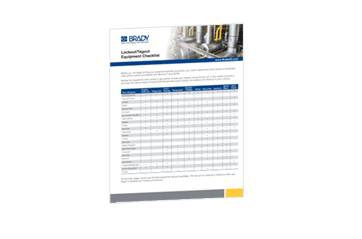
Learn what equipment you need to effectively use lockout tagout in your facility with our downloadable checklist.
Download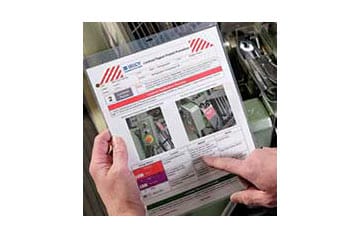
See what other Safety Managers are most commonly asking about the lockout tagout standard.
View FAQ's